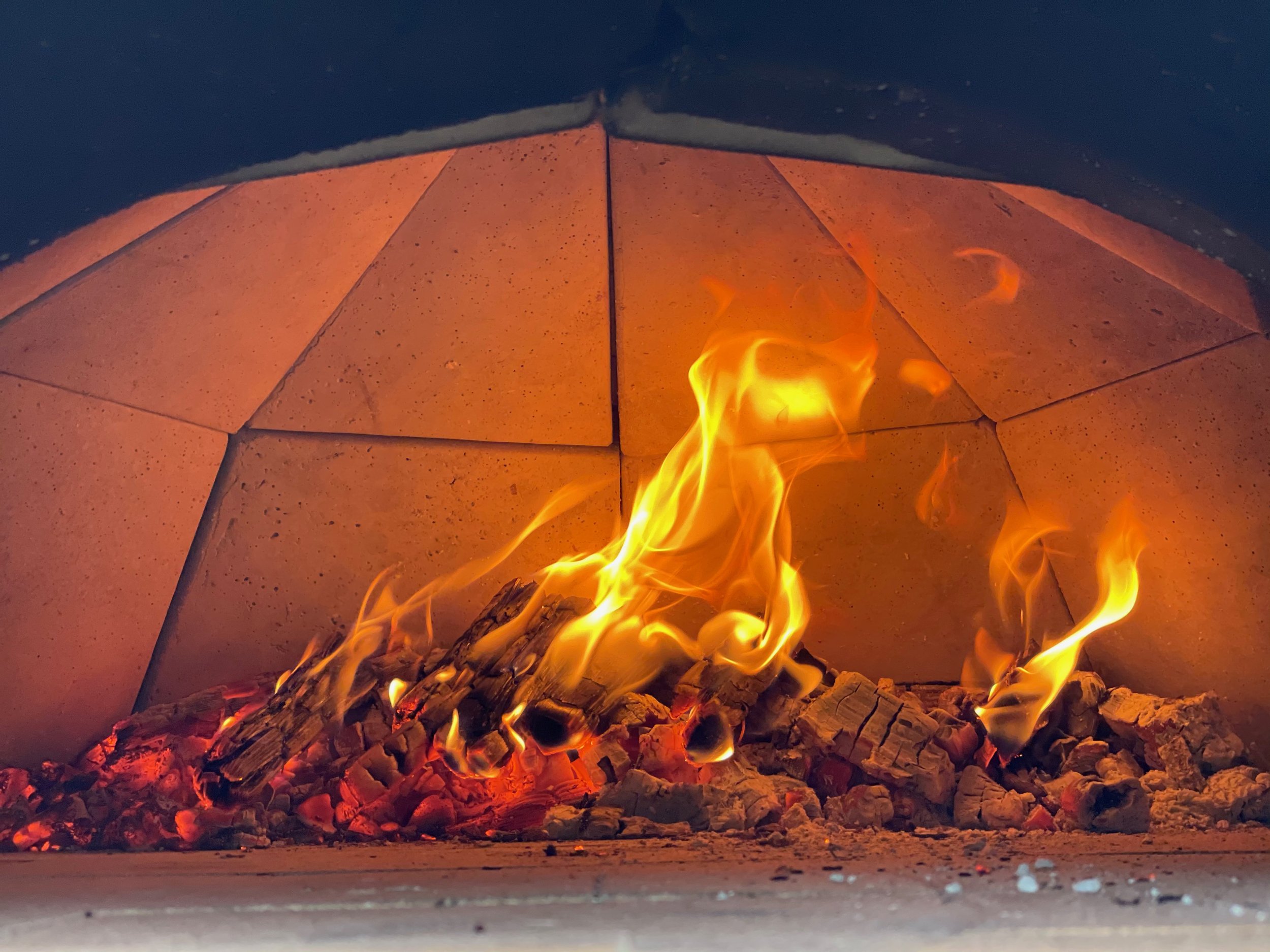
agnes outdoors
AFTER A FEW UNIVERSITY SUMMERS OF CHEFFING FOR A LOCAL ARTISAN PIZZA COMPANY, THE OWNER DECIDED THEY’D LIKE TO MANUFACTURE AND SELL THEIR OWN PIZZA OVENS. THE AIM: A SELF BUILD PIZZA OVEN KIT BYPASSING THE DIFFICULT PARTS OF TRADITIONAL STONE OVENS.
Agnes Outdoors, Product Designer, Freelancing, Two Projects, 2019/20 & 2024
consultation
quotation
concepting
design proposal
design for manufacture
drawing pack
tooling design
content creation
rESEARCH, CONCEPT DEVELOPMENT, FULL SCALE MODELLING AND VISUALISATION ENSURED THE CLIENTS NEEDS WERE MET for the first oven.
After 6 majorly different concepts, and 5 major iterations to this design, the octagonal igloo oven was chosen as the internal structure. Once insulated and rendered this oven would have the required strength, while the divides would allow for thermal expansion and contraction well, and be based around easy to operate, fast and affordable mould tools.
final proposal
Before going into tooling design, the final structure and geometry of the oven were signed off, with some wireframes and renders to assist the client in understanding the product.
tOOLING DESIGN
Although more of a challenge was faced in consistency and tolerances, sheet metal tooling made the project far more affordable, and through some prototyping the designs were perfected. The majority of the oven could be produced with simple tools, while the front block required a more complex arrangement.
FULL SELF BUILD KIT
Before going into tooling design, the final structure and geometry of the oven were signed off, with some wireframes and renders to assist the client in understanding the product.
Where did the project lead?
oven 1, oven 2, oven 3?…
With oven one on the market and batch produced to order, the tooling and first prototype for a larger scale second oven has been completed, and a third project for a different market is in concepting.